Mastering Precision: The Ultimate Guide to Fiber Laser Cutting Machines
- Pratik Patel
- Feb 27, 2024
- 3 min read
In the realm of manufacturing, precision is paramount. Whether crafting intricate components for aerospace engineering or producing finely detailed designs for artistic purposes, the ability to cut with exactitude can make all the difference. In recent years, fiber laser cutting machines have emerged as a game-changer in the world of precision cutting, offering unparalleled accuracy, speed, and versatility. In this comprehensive guide, we delve into the intricacies of fiber laser cutting machines, exploring their technology, applications, advantages, and tips for mastering their capabilities.
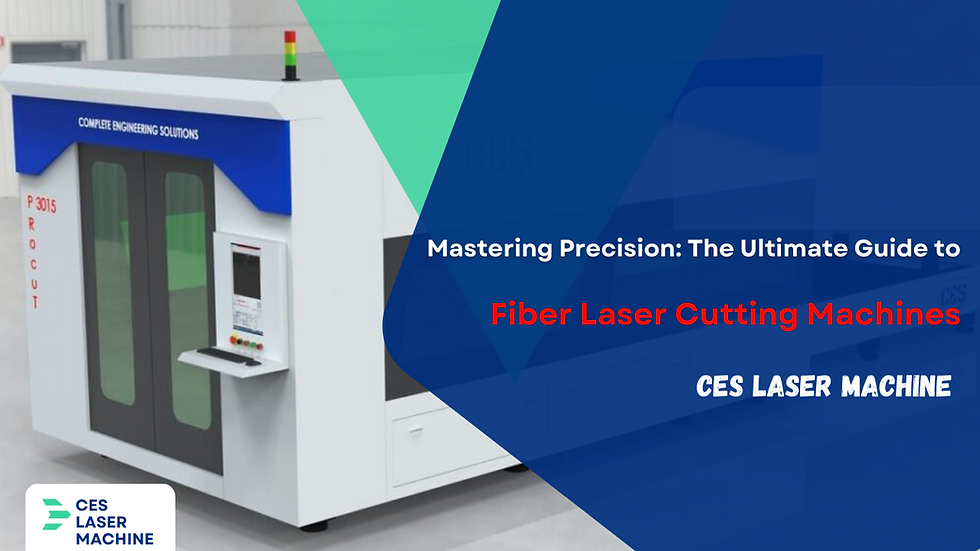
Understanding Fiber Laser Cutting Technology
At the heart of a fiber laser cutting machine lies advanced laser technology. Unlike traditional CO2 lasers, which rely on gas mixtures to generate the laser beam, fiber lasers utilize optical fibers doped with rare-earth ele
ments such as ytterbium. These fibers serve as the medium for amplifying and transmitting the laser beam with exceptional efficiency and precision.
Fiber laser cutting machines harness this laser energy to precisely cut through various materials, including metals like steel, aluminum, brass, and copper, as well as non-metallic materials like plastics, composites, and ceramics. The focused laser beam melts, vaporizes, or burns through the material, guided by computer-controlled motion systems to achieve intricate shapes and contours with micron-level accuracy.
Applications of Fiber Laser Cutting
The versatility of fiber laser cutting machines makes them indispensable across a wide range of industries:
Automotive: From precision-cutting sheet metal components to fabricating intricate chassis parts, fiber laser cutting machines play a vital role in automotive manufacturing.
Aerospace: In the aerospace industry, where lightweight materials and stringent tolerances are critical, fiber lasers enable the precise fabrication of aircraft components, engine parts, and structural elements.
Electronics: Fiber laser cutting is used in electronics manufacturing for producing intricate circuit boards, thin metal enclosures, and precision components for electronic devices.
Medical Devices: The medical sector relies on fiber laser cutting for manufacturing surgical instruments, implants, medical device components, and custom prosthetics with high precision and cleanliness.
Architectural and Decorative Metalwork: Fiber lasers are employed in architectural metalwork and decorative applications to cut intricate designs, patterns, and lettering on metal surfaces for signage, sculptures, and interior décor.
Advantages of Fiber Laser Cutting Machines
Fiber laser cutting machines offer several distinct advantages over other cutting methods:
High Precision: Fiber lasers deliver exceptionally precise cuts with minimal kerf width, enabling intricate designs and tight tolerances.
Speed and Efficiency: With high-speed cutting capabilities, fiber lasers can process materials quickly, leading to improved productivity and reduced production times.
Versatility: Fiber lasers can cut a wide range of materials, including metals, plastics, and composites, making them suitable for diverse applications.
Minimal Maintenance: In contrast to alternative cutting methods, fiber lasers boast fewer moving components, leading to decreased maintenance needs and less downtime.
Energy Efficiency: Fiber lasers are more energy-efficient than CO2 lasers, consuming less power while delivering comparable or superior performance.
Tips for Mastering Fiber Laser Cutting
To harness the full potential of fiber laser cutting machines, consider the following tips:
Optimize Parameters: Fine-tune cutting parameters such as laser power, cutting speed, and focal length to achieve the desired cut quality and efficiency for specific materials and thicknesses.
Material Preparation: Ensure that the material to be cut is clean, flat, and properly secured to minimize vibrations and distortion during cutting.
Maintain Machine Integrity: Regularly inspect and maintain the machine components, including optics, nozzles, and assist gases, to ensure optimal performance and longevity.
Utilize Software Tools: Take advantage of advanced CAD/CAM software to design intricate parts, generate cutting paths, and optimize nesting layouts for maximum material utilization.
Safety Precautions: Adhere to safety guidelines and wear appropriate personal protective equipment (PPE) when operating fiber laser cutting machines to prevent accidents and injuries.
Conclusion
Fiber laser cutting machines represent a pinnacle of precision engineering, offering unmatched accuracy, speed, and versatility in the realm of manufacturing and fabrication. From automotive and aerospace industries to electronics, medical devices, and beyond, fiber lasers have revolutionized the way we cut and shape materials with precision and efficiency. By understanding the underlying technology, applications, advantages, and best practices for mastering fiber laser cutting, manufacturers can unlock new possibilities for innovation, customization, and quality in their products. So, embrace the power of fiber laser cutting and embark on a journey towards mastering precision in manufacturing.
Comments